Poka yoke ist ein japanischer Begriff, der so viel wie “Fehlersicherung” oder “Fehlervermeidung” bedeutet. Es handelt sich um eine Methode der Qualitätskontrolle, die darauf abzielt, Fehler oder Irrtümer von vornherein zu vermeiden, indem Prozesse und Systeme so gestaltet werden, dass Fehler nur schwer oder gar nicht auftreten können. Das Konzept des Poka Yoke wurde von dem japanischen Ingenieur Shigeo Shingo im Rahmen des Toyota-Produktionssystems entwickelt und seitdem von vielen anderen Unternehmen auf der ganzen Welt als Mittel zur Verbesserung der Qualität und Effizienz in der Fertigung und anderen Prozessen übernommen.
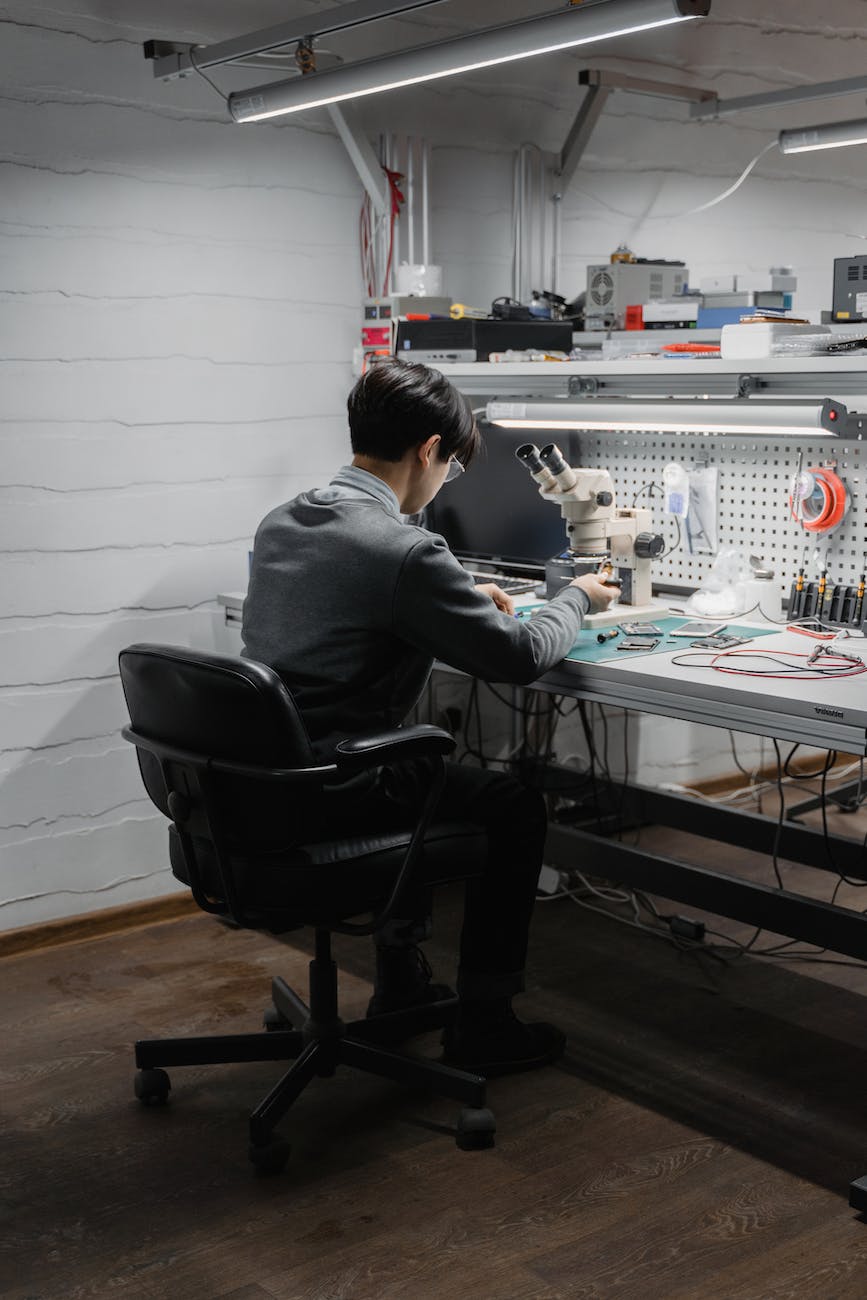
Vorteile und Ergebnisse von Poka Yoke
Zu den Vorteilen des Poka Jochs gehören:
- Verbesserte Qualität: Poka-yoke trägt dazu bei, dass Produkte oder Dienstleistungen den geforderten Qualitätsstandards entsprechen, indem es Fehler vermeidet. Dies kann zu weniger fehlerhaften Produkten und höherer Kundenzufriedenheit führen.
- Gesteigerte Effizienz: Poka-yoke kann zur Rationalisierung von Prozessen beitragen, indem es Nacharbeiten oder Korrekturen überflüssig macht, was Zeit sparen und die Effizienz steigern kann.
- Kosteneinsparungen: Durch die Vermeidung von Mängeln und Fehlern kann Poka-Yoke dazu beitragen, die mit der Korrektur von Fehlern oder der Nachbearbeitung von Produkten verbundenen Kosten zu senken.
- Verbesserte Sicherheit: Poka-Yoke kann zur Verbesserung der Sicherheit beitragen, indem es Unfälle oder Verletzungen verhindert, die aufgrund von Fehlern oder Mängeln auftreten können.
- Gesteigerte Wettbewerbsfähigkeit: Durch die Verbesserung von Qualität und Effizienz kann Poka-Yoke Unternehmen helfen, auf ihren Märkten wettbewerbsfähiger zu werden.
5 Arten von Poka Yoke
Es gibt mehrere Arten von Poka-Yoke, die zur Vermeidung von Fehlern oder Mängeln in einem Prozess eingesetzt werden können. Einige gängige Typen sind:
- Kontakt-Methode: Bei dieser Art von Poka-Yoke besteht ein physischer Kontakt zwischen dem Bediener und dem Gerät oder dem Prozess. So kann beispielsweise eine Vorrichtung verwendet werden, um die Hand des Bedieners an die richtige Stelle zu führen, oder es kann ein Sensor eingesetzt werden, um zu erkennen, ob ein Teil richtig ausgerichtet ist.
- Festwert-Methode: Bei dieser Art von Poka-Yoke wird ein bestimmter Wert oder eine Reihe von Werten festgelegt, die erfüllt sein müssen, damit der Prozess fortgesetzt werden kann. So kann beispielsweise eine Maschine so programmiert werden, dass sie anhält, wenn die Temperatur eines Prozesses einen bestimmten Schwellenwert überschreitet.
- Bewegungs-Schritt-Methode: Bei dieser Art von Poka-Yoke muss der Bediener eine bestimmte Abfolge von Handlungen ausführen, damit der Prozess fortgesetzt werden kann. An einem Fließband kann es beispielsweise erforderlich sein, dass der Bediener eine Reihe von Schritten in einer bestimmten Reihenfolge ausführt, z. B. ein Teil vor einem anderen einbaut.
- Warnmethode: Bei dieser Art von Poka-Yoke wird der Bediener gewarnt, wenn ein Fehler oder Defekt festgestellt wird. Beispielsweise könnte eine Maschine so programmiert werden, dass ein Alarm ertönt, wenn ein Teil nicht richtig ausgerichtet ist.
- Selbstkontrollierende Methode: Bei dieser Art von Poka-Yoke prüft sich das Gerät oder der Prozess selbst, um sicherzustellen, dass es korrekt funktioniert. Eine Maschine kann beispielsweise so programmiert werden, dass sie regelmäßig einen Selbstdiagnosetest durchführt, um sicherzustellen, dass sie ordnungsgemäß funktioniert.
Poka Yoke-Anwendung
Poka-yoke kann in einer Vielzahl von Umgebungen und Branchen eingesetzt werden, z. B. in der Fertigung, im Dienstleistungssektor und in Büroumgebungen. Einige Beispiele dafür, wie Poka-Yoke angewendet werden kann, sind:
- Herstellung: In der Fertigung kann Poka-Yoke eingesetzt werden, um Fehler zu vermeiden, z. B. den Zusammenbau eines Produkts mit den falschen Teilen, die Verwendung des falschen Werkzeugs oder den fehlerhaften Einbau eines Teils. So kann beispielsweise eine Vorrichtung verwendet werden, um die Hand des Bedieners an die richtige Stelle zu führen, oder es kann ein Sensor eingesetzt werden, um zu erkennen, ob ein Teil richtig ausgerichtet ist.
- Dienstleistung: Im Dienstleistungsbereich kann Poka-Yoke eingesetzt werden, um Fehler zu vermeiden, z. B. die falsche Dienstleistung zu erbringen, die falsche Ausrüstung zu verwenden oder einen notwendigen Schritt zu vergessen. So könnte beispielsweise eine Checkliste verwendet werden, um sicherzustellen, dass alle erforderlichen Schritte ausgeführt werden, oder es könnte ein Warnsystem eingerichtet werden, das den Bediener im Falle eines Fehlers alarmiert.
- Büro: In einer Büroumgebung kann Poka-Yoke verwendet werden, um Fehler zu vermeiden, z. B. die Eingabe falscher Daten, das Vergessen eines notwendigen Schritts oder das Senden eines Dokuments an die falsche Person. So kann beispielsweise ein Softwareprogramm zur Überprüfung der Richtigkeit der Dateneingabe eingesetzt werden, oder es kann eine Checkliste verwendet werden, um sicherzustellen, dass alle erforderlichen Schritte durchgeführt werden.