かいぜん(継続的改善)
カイゼンとは何か? 直訳すると「改善」、一般的には「継続的改善」を意味する日本語です。 たとえ業務が滞ったとしても、時間をかけて改善した方がいいというのが中心的な考えです。 極端な話ですが、この経営理念が現代ではどのように機能するのか、詳しく説明します。 カイゼンとは、簡単に言うと、企業内のすべての業務と従業員の機能を永続的に改善することに焦点を当てたものです。 この段階的なステップの大小は問いませんが、ひとつだけ非常に重要なことは、改善は継続的な事業でなければならないということです。 キーポイント カイゼンとは、「より良い方向への変化」という意味です。 段階的な継続的改善を実施するために使用されます。 時間をかけて改善したほうがいいに決まっています。 企業文化全体を巻き込む必要があります。 カイゼンの歴史 カイゼンは、第二次世界大戦後まもなく、アメリカの経営学や品質管理の専門家の影響もあって、日本の企業で初めて使われるようになった。 時間と資源がない中で、抜本的な改革を行うよりも、既存の人材や技術の段階的な改善を追求する方が得策だったのです。 それ以来、「カイゼン」は、トヨタ生産方式を筆頭に、世界中の多くの企業で活用され、洗練されてきました。 さらに、世界中の生産・製造以外のさまざまな用途に発展しています。 カイゼンはどのように機能するのか? カイゼンの推進者であるトヨタでは、従業員一人ひとりが問題を発見した場合、あるいはプロセスをより良くする方法を提案することができた場合、生産を停止することが奨励されます。 このような場合、組み立てを中断し、チームで問題を評価し、改善した上で、再び組み立てを開始します。 生産スピードを落として漸進的な改善を行うことは、直感に反すると思われるかもしれません。 しかし、納品までのあらゆる時間を活用して製品をより良いものにするJIT(Just-In-Time Production)と呼ばれるものが機能しています。 カイゼンやJITでは、予定より早く生産を終えてしまうと、その時間をより良い製品を作るために使わなかったことになってしまいます。 トヨタにとって、これはプロセスを継続的に改善し、製品の価値を高める機会を逃すことになる。 社員が自由に悩みを打ち明けたり、付加価値をつけたりすることで、企業は社員全員のユニークな視点から、より高い可視性を得ることができるのです。 これにより、企業はオペレーションを完全に可視化することができるようになりました。 従業員や経営陣が頻繁に漸進的な改善を行うことに慣れるにつれ、企業はプロセスの早い段階で問題を解決するようになり、しばしば製品が組立ラインで生産される前に問題を解決するようになりました。 継続的改善の目標 カイゼンは方法であり、目標ではないことを理解する必要があります。 カイゼンを達成するのではなく、あなたとあなたのチームが選んだ特定の目標を達成するために、企業レベルでカイゼンを実施するのです。 それは、無駄の排除、品質の向上、生産性の向上、物流の効率化など、さまざまなものがあります。 カイゼンはあらゆる企業の目標に適用でき、この2つの主要な目標に焦点を当てることで機能します: すべての業務を改善する:この継続的な改善プロセスは、ビジネス内のすべての機能を巻き込む必要があります。 会社全体の中で、どの部署もつながっている。 もし、一部の部門やリーダーシップの領域が継続的改善の取り組みに参加していない場合、特定の変更が特定の部門にのみ利益をもたらし、会社全体には利益をもたらさないかもしれません。すべての労働者を巻き込む:カイゼンは、チームと企業文化に大きく依存します。 それは、会社で働くすべての人の才能と知識を活用することに重点を置くことです。 チームワークとエンゲージメントが十分でなければ、企業はオペレーションを改善するための貴重な洞察と機会を失うことになります。 カイゼンの5原則 他のビジネス哲学と同様に、カイゼンにも特定の基本原則があり、それを遵守します。 これらの原則のうち、1つでも2つでも外れている企業は、カイゼンの取り組みが台無しになる可能性が高いです。 この5つの原則は お客様を知る:企業は、顧客のニーズを把握する必要があります。 顧客を知っていれば、その顧客が何に価値を見出し、何にお金を払うかを理解することができます。 このような知識があれば、企業は適切な製品をより良い価値で提供することができるようになるのです。流れに任せる:無駄は、優れたプロセスフローの宿敵です。 組織の中に無駄があれば、時間とお金が効率的に活用されていないことになります。 オペレーションからすべての無駄を取り除くことは不可能に思えるかもしれませんが、それは常にカイゼンの目標になります。ゲンバに行く:Gemba」を直訳すると、「本当の場所」。 リーダーシップや方向性は、生産の実態に即したものである必要があります。 リーダーは「本場」に行って自分の目で確かめないと、オペレーションを理解できない。エンパワーピープル:これは、部下を適切に組織化することです。 作業者が相反する機能を持ち、効果的なチームとして機能しない場合、改善の可能性は極めて低くなります。 カイゼンのリーダーシップは、従業員一人ひとりのスキルを認識し、人々に力を与えるツールを提供することである。透明性を確保する:改善や方向性に関するデータや知識は、隠すことなく透明性を持たせる必要があります。 より多くの情報を収集することで、あなたやあなたの組織の誰かが、効果的で長続きする改善を実施できる可能性が高くなります。 カイゼン文化とは? カイゼンは、企業文化として定着していないと効果がありません。 もし、会社全体が漸進的・継続的な改善の追求に関与していなければ、カイゼンの取り組みは必ず失敗することになります。 しかし、組織全体の集合知と才能を動員すれば、継続的改善は企業構造の中で強力な効果を発揮します。 […]
主要業績評価指標(KPI)
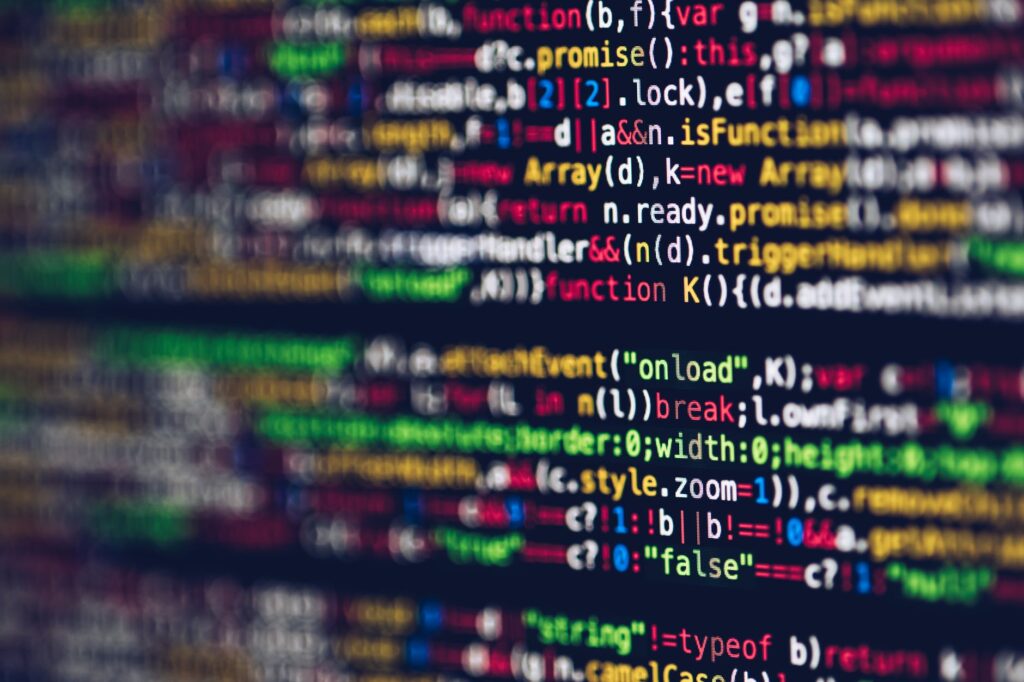
KPIとは何ですか? 重要業績評価指標(KPI)とは、企業が設定された目標や目的に対するパフォーマンスを追跡するために使用する、定義された指標です。 販売統計、品質出力、廃棄物の軽減など、あらゆるものが含まれます。 製造業では、KPIによって、業界のリーダーたちは、業務、財務、顧客のパフォーマンスに関する貴重な洞察を収集することができます。 これらのインサイトは、製造業のKPIダッシュボードに整理され、迅速かつ容易に知識を吸収することができます。 製造業のKPIは、2つの重要な要素で構成されています: 実際の業績:事業がどのように推移しているか意図した業績:事業の業績がどの程度であるべきか。この2つの要素により、あらゆる産業は、ビジネスとオペレーションの健全性の基礎となるものを追跡・監視することができ、KPIは産業間の貴重なツールとなっています。 キーポイント KPIは、設定された目標や目的と比較してパフォーマンスを測定するために使用されます。 実際のパフォーマンスと意図したパフォーマンスという2つの重要な要素で構成されています。 KPIには3つのカテゴリーがあります:プロセス指標」「財務指標」「顧客指標」です。 正確なKPIのためのデータは、定量的かつ客観的である必要があります。 VKSのような製造ソフトウェアを使って、効率的かつ自動的にKPIを追跡・測定しましょう。 3種類のKPI企業が使用する指標は無限にあるように見えますが、すべてのKPIは3つの包括的なカテゴリに分類されます:プロセス指標」「財務指標」「顧客指標」です。 プロセスメトリクスプロセスメトリクスは、オペレーションのパフォーマンスに焦点を当てます。 例えば、製造業の場合、企業は不良品の発生率や割合を測定することができます。 この場合、この数値を許容範囲内に収めるか、可能であれば欠陥を完全に除去することが目標になります。 プロセスメトリクスの例としては、サイクルタイムやタクトタイムがあります。 さらに、欠陥率を100万機会あたり3.4欠陥まで下げることはシックスシグマの特徴ですが、これはプロセスKPIを追跡しなければ観察することができませんでした。 財務指標財務指標は、どれだけのお金が使われ、節約され、生産されているかに焦点を当てています。 これには、売上総利益率や運転資本などの指標も含まれます。 各部門の財務KPIを分解することで、企業はどこにお金が使われているのか、どの程度使われているのか、そしてROIをより細かく把握することができます。 カスタマーメトリクスカスタマーメトリクスは、顧客満足度、顧客維持率、顧客効率の観点からパフォーマンスを観察します。 製品の価値は、顧客や市場によって決定されることが多いため、この視点に立ったKPIは、企業が顧客に対してどの程度のパフォーマンスを発揮しているのか、鋭い洞察力を与えてくれるのです。 リードタイムなどの指標は、注文後、顧客が製品を受け取るまでにかかる時間を測る優れた方法です。 これらのカテゴリーは、それぞれ他のカテゴリーとある程度相互作用しています。 生産パフォーマンスは、必ず財務パフォーマンスや顧客パフォーマンスに影響を与えるので、すべての部門とそのパフォーマンスは本質的につながっていることがわかります。 なぜ製造業のKPIを使うのか? 製造業における成功は、指標となる目標との比較によってのみ知ることができる。 そうでなければ、企業は特定のオペレーションが低業績なのか高業績なのかを判断することができない。 例えば、1年間に10個の製品を生産することは、宇宙航空メーカーにとっては良い指標かもしれませんが、消費財メーカーにとっては絶望的な数字となります。 すべてのKPIの底にある2つの基本的な質問です: 目的を達成できたのは何回目か?目標まであとどれくらいか? KPIは、企業が製造オペレーションの複雑さを十分に理解することを可能にします。 目標を達成し、ビジネスのパフォーマンスを把握するために、KPIは欠かせないツールです。 成功も失敗も、その原動力であり、シグナルである 製造業のKPIを成功させるための4つのルールKPIの作成と追跡を成功させることは、想像以上に簡単です。 この4つのルールに従うだけで、最も正確なデータを取得することができます。 目標を明確にするまず自問自答するのは、「自分は何を目指しているのか」ということです。 先ほどの航空宇宙と消費財の例で考えてみましょう。 目標を明確にすることで、業界における適切なパフォーマンスレベルを突き止めることができます。 気をつけなければならないのは、目標は現実的なものである必要があるということです。 達成可能な目標を設定することで、手の届かない目標を設定するよりも、より早く改善、進歩することができます。 客観的に数値化できる明確なパラメータを設定する。数値化できる目標を選ぶことが、KPIの客観性と正確性を保つ最適な方法です。 数値に基づく指標を設定することで、積極的に成果を測定し、時系列で比較することが可能になります。 結局のところ、すべては数値化できるのです。 顧客満足度のような主観的な指標も、統計や大規模なサンプル調査によって数値に落とし込むことができる。 強力なソースからデータを取得する製造業のKPIを追跡するインテリジェントな方法は、VKSデジタル作業指示書のような専用製造ソフトウェアを使用することです。 生産時間や品質を手作業で記録するのではなく、作業指示ソフトウェアによって、リアルタイムに記録される自動化されたプロセスになります。 オペレーターが作業指示書に沿って作業を進めると、VKSは裏で主要な指標をトラッキングし、必要に応じてオペレーターがデータを入力し、フィードバックすることも可能です。 データ収集と報告の適切なタイミングを計る当然のことながら、KPIをどのように収集し報告するかは、時間が重要な役割を果たします。 運用や報告スケジュールによっては、月単位や週単位でKPIを報告したい場合もあります。 一方、KPIのためのデータ収集は、必要な頻度で行う必要があります。 これにより、自分のパフォーマンスを実況中継し、最新の情報を入手することができます。
リードタイム
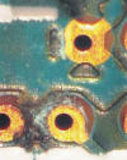
リードタイムとは リードタイムとは、お客様が注文してから製品が納品されるまでの期間のことです。 購入プロセスの開始時に始まり、取引の完了時に終了します。 リードタイムは、多くの意味で、製造プロセス全体に対するお客様の経験値です。 お客さまは注文をし、商品の到着を待ち、決済して取引を完了します。 製造業では、リードタイムを常に見直すことが重要です。なぜなら、リードタイムはお客様の経験を評価する方法だからです。 生産工程やサイクルタイムが記録的な速さになったとしても、リードタイムが厳密にモニターされていなければ、顧客はその恩恵を受けられないかもしれません。 リードタイムとその仕組みについて、詳しく見ていきましょう。 キーポイント リードタイムとは、お客様が注文してから、注文品を受け取り、決済が完了するまでの時間を指します。 通常、リードタイムはサイクルタイムと納期を足したものである。 リードタイムの増減には、さまざまな要因があります。 材料不足、サイクルタイムの遅れ、労働問題など、さまざまな要因があります。 リーン生産方式やスマートな在庫管理など、近代的な生産方式を導入することで、リードタイムを短縮することができます。 リードタイムの計算方法 リードタイムの計算は、かなり簡単です。 お客様が注文してから、どのくらいで商品が届くのでしょうか? しかし、製造システムによっては、計算が異なることがあります。 一般的なプッシュ型生産方式に見られるような、すでに確立された大量の在庫がある状態でリードタイムを計算する場合、リードタイムは配送または輸送時間のみから導き出されます。 ATO(Assemble to Order)やMTO(Make to Order)のようなプル型生産システムからリードタイムを計算する場合、2つのデータが必要です: 製品のサイクルタイム(CT)そのユニットを輸送するために必要な納期(DT)。このようにLead Timeを計算すると、Cycle Timeは顧客が注文した時点で開始する必要があります。 これを踏まえて考えてみましょう。 あなたは、高品質のカスタマイズされた木製野球バットを製造しているとします。 お客様は、お客様のウェブサイトで注文し、商品を待ちます。 あなたのウッドバットの納期は2日で、ウッドバットのデザイン、製作、カスタマイズに丸2日かかります。 この場合、リードタイムは次のように計算されます: ct [2] + dt [2] = lt [4] です。 お客様のお手元に届くまでのリードタイムは4日程度とお考えください。 この方程式をさらに細かく分解して、リードタイム全体を構成する特定のアクションを特定することができます。 これには、複数の輸送ライン、設計段階、生産段階などが含まれることがあります。 タクトタイム vs. サイクルタイム vs. リードタイム リードタイムを計算できるようになったので、この情報を他のリーン生産指標と一緒にまとめることができます。 タクトタイム:需要に対応するために必要な生産時間。サイクルタイム:1つのアイテムの実際の生産時間。リードタイム:お客様が注文してから、注文品を受け取り、支払いが完了するまでの時間。リードタイムにはタクトタイムの影響を受けるサイクルタイムが含まれるため、これら3つの指標は密接に関連しています。 タクトタイム(需要)は、最適なサイクルタイム(生産速度)を決定し、それがリードタイム(顧客が製品を受け取るまでの時間)に影響します。 この3つがどのように作用しているかを理解すれば、他の要素がリードタイムにどのような影響を与えるかを確認することができるようになります。 また、そのことによって、時間を短縮し、お客様の期待に応えるための創造的な方法を見つけることができます。 リードタイムに影響を与える要因とは? […]
リーン・マニュファクチャリング
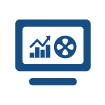
リーン・マニュファクチャリングとは? リーン生産方式とは、製造業が無駄を省き、顧客価値を最適化し、企業の生産性を高めるために用いる生産手法である。 付加価値を高める要素に焦点を当て、無駄を省く活動を行うことで、企業はより多くの価値を創造し、より高い業務効率を追求することができます。 本来、リーン・マニュファクチャリングはWin-Winのシナリオである。 核となる原則に注意深く従えば、リーン生産はコストを下げ、価値を高めることで、組織と市場の消費者にとって有益なものとなります。 キーポイント リーン生産とは、製品やサービスの価値を高めながら、無駄な活動を削減するプロセスです。 最も価値のある生産要素は、顧客に価値をもたらすものである。 リーン生産方式の基本原理は、トヨタ生産方式(TPS)にヒントを得ています。 リーン・マニュファクチャリングは、適切なバランスを見つけることです。 無駄をできる限り省くが、リーンを超えて生産に支障をきたさないようにする。 リーンの簡単な歴史 リーン生産方式は、1948年から1975年の間にトヨタ生産方式(TPS)によって初めて開発されました。 それ以来、リーンは、企業が模範とする非常に効率的な生産モデルとして、世界的に有名になりました。 トヨタ自動車の技術者である大野耐一と豊田英二は、主に自動車産業における無駄な在庫を軽減する方法としてこのシステムを作りましたが、今では多くの産業において、無駄を軽減し価値を高める他の方法と実践を包含するまでに成長しました。 リーンに影響を受けた生産手法の例として、カンバン、カイゼン、リーンシックスシグマ、DMAIC(定義、測定、分析、改善、管理)、DMADV(定義、測定、分析、設計、検証)などがあります。 それぞれ、製造環境におけるリーン手法のさらなる定義と強化に貢献します。 バリューとは何か? リーン・マニュファクチャリングを明確に理解するためには、顧客の視点から価値を理解する必要があります。 もし、ビジネスが顧客に価値を提供しないのであれば、ビジネスは成り立たない。 このように、リーン生産方式では、価値が最優先されるのです。 生産ライン内の価値は、3種類の活動に分かれる: 付加価値:消費者に価値を提供する活動である。 便利な機能、製品サポートなどを紹介します。事業付加価値:事業に対して直接的に価値を提供しつつ、顧客に対して間接的に価値を提供する活動です。 これには、保守、点検、データ保存などの活動が含まれます。非付加価値:消費者が目にしない、必要としない、そして/またはお金を払う気がない、不必要な活動です。 非付加価値活動は、リーン計画で最初に排除されるものの一部です。リーン生産方式では、常に消費者の視点を通して価値を考えます。 商品の価値を決めるのは、消費者です。 企業はその目標を達成するために、製品やオペレーションを適応させなければなりません。 消費者にとって直接的または間接的に付加価値をもたらさないものは、廃棄物とみなされ、除去されるべきです。 リーン生産方式の5つの原則 リーン・マニュファクチャリングは、以下の5つの原則を特徴としています。 価値を特定する:企業は、何が顧客に価値をもたらすかを特定する必要があります。 価値が明らかになれば、企業は顧客のニーズを満たす製品を設計する一方で、そうでない機能を削除することができるようになります。バリューストリームをマップする:バリューストリームとは、製品のライフサイクル全般を指します。 設計、材料、製造・組立、販売、お客様の使用、そして最終的な製品の廃棄までを含みます。 製品のバリューストリームをマッピングした後、メーカーはバリューストリームの中で付加価値のない要素やステップを削除することができます。フローを作る:制作にフローがなければ、時間を浪費していることになります。 アイテムは、バリューストリームを途切れることなく移動する必要があります。 リーン生産者は、効率的にオペレーションを整理して、流れ作業をしています。エスタブリッシュ・プル:この原則は、明確な需要がある場合にのみ、企業がその商品を生産することを要求するものです。 生産に流れを作るのと同じように、生産からお客様への移行も、どの時点でも滞らないようにしなければなりません。 市場に商品を送り込むのではなく、市場が生産ラインから商品を引き抜くため、大量かつ無駄な在庫を抱える必要がないのです。完璧を求める:リーン生産方式がビジネスに大きな影響を与えるには、企業文化が関与する必要があります。 すべての社員とシステムが、リーン・プラクティスを組織全体に広く適用し、完成させることを目指す必要があります。 廃棄物とは何か? 製造現場における「リーン」とは何かを正確に理解するためには、無駄とそれがどのように発生するかを明確に理解する必要があります。 トヨタ生産方式(TPS)によると、無駄は3つに分けて考えることができる。 ムダ(無用の長物):現在、廃棄物に関する議論の多くは、無駄な慣習を中心に行われています。 これらは、顧客に付加価値を与えないあらゆる活動である。 これは、ペーパーワークから非効率なロジスティックプランニングに至るまで、あらゆるものが含まれます。 製品やサービスの価値の流れの中で、無駄を生み出す活動や無駄な活動を排除・削減することである。ムリ(過重負担)です:ムリとは、操作の補助システムを外しすぎた結果です。 お客さまに直接付加価値を与えないシステムもありますが、それでもオペレーションには有用なものです。 真のリーン・マニュファクチャリングには、現代の製造業の課題に耐えうる柔軟性と弾力性が必要です。ムラ(凸凹):生産ラインは、バランスをとって流すことが必要です。 そうでなければ、必然的に非効率が発生します。 ムラは、顧客の需要(タクトタイム)や、製品ごと、作業者ごとの工程・サイクルタイムなど、生産のさまざまな領域で見られる。無駄を理解し、カットすることは、バランスをとることです。 リーン手法に取り組む企業は、無駄を省くべきですが、経営に支障をきたすほど深刻なものではありません。 リーンの8つの無駄 無駄をより深く、バランスよく理解するためには、「リーンの8つの無駄」を通して理解するのがよいでしょう。 これらは、DOWNTIMEという適切な頭文字を使って覚えることができます。 […]
リーンシックスシグマ
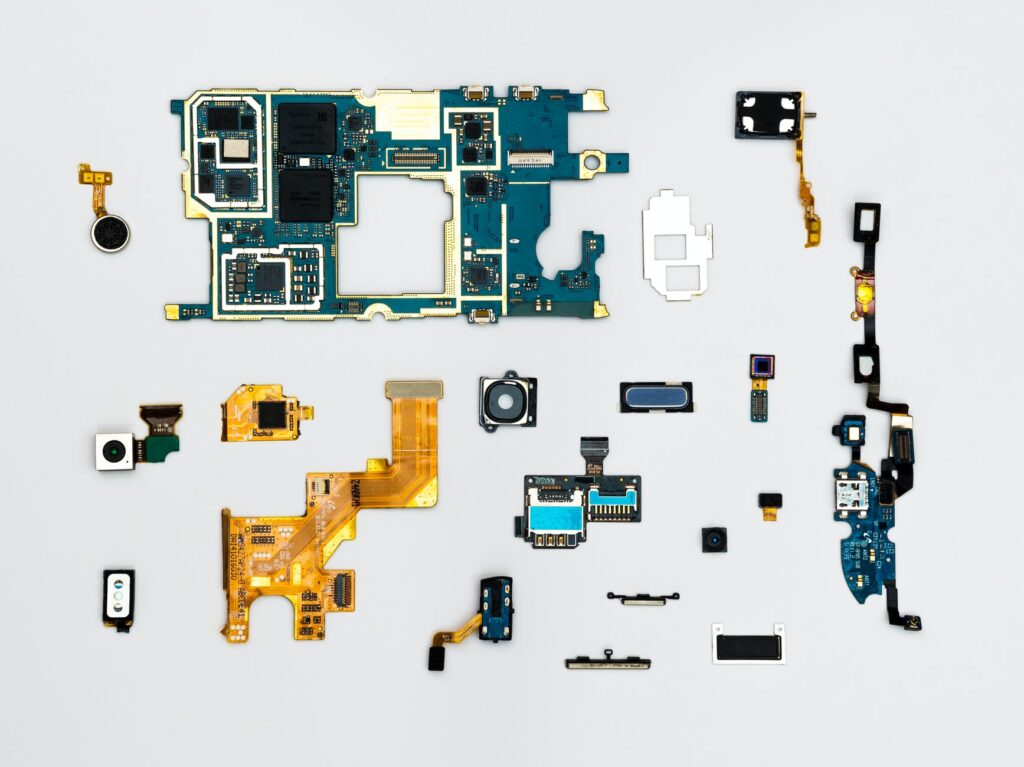
企業は長年にわたって経営哲学を混ぜ合わせてきたため、リーン生産方式とシックスシグマの方法論が互いに補完し合ってうまく機能していることを多くの企業が発見しています。 こうして、リーンシックスシグマは、バラツキとムダの両方を減らすという二重の目的を持って、徐々に採用されていきました。 キーポイント LSSは、6Sのデータベース・プロセスとリーンの需要ベース・プロセスを融合させたものです。 LSSで生産ラインを中心としたプロセスフローをリアルタイムに効率化 リーン・シックスシグマとは? リーン・マニュファクチャリングの基本 リーン生産方式とは、生産工程から可能な限り無駄を排除し、生産物の価値を最大限に維持することを基本とする手法です。 リーンの原理には、企業内のワークフローや社会組織を改善するためのさまざまなテクニックやツールが含まれます。 また、「ポカヨケ」のようなツールは、生産サイクルのボトルネックの特定に非常に有効です。 リーンの基本は、工業生産における最も一般的な8つの無駄を列挙したDOWNTIMEという頭文字に言及しています: Defect – エラーや失敗過剰生産 – 販売可能な量以上の製品を作ることWaiting – 機械や演出を待っている時間。活用されていない人材 – 活用されていない社員のスキル輸送 – 物流・ロジスティクス在庫-売れ残った製品は倉庫に置くとコストがかかるモーション – リソースの誤用と組立ライン内の動きExtra Processing – 価値を提供しない過剰なエンジニアリングこのような無駄を洗い出し、生産から排除することがリーン生産方式の最大の目標です。 ムダを発見する手段は、主に生産ラインを実際に歩いてみて、質的に何が起こっているのかを「自分の目で確かめる」ことです。 シックスシグマの基礎知識 シックスシグマは、統計分析に基づく問題解決プロセスの活用により、製品のばらつきや不良を減らすことに主眼を置いています。 シックスシグマで使われるツールには、DOE、パレート図、バリューストリームマップなどがあります。 シックスシグマプロセスの原則は、頭文字をとってDMAICを指します: お客様の視点からプロセスの境界と期待値を定義する。現在存在するプロセスの定量的な性能を測定する。相関するデータを分析し、根本的な問題を特定する。代替ステップを開発し、テストすることでプロセスを改善する定期的なメンテナンスにより、プロセスの継続的な成功をコントロールする。DMAICメソッドで定義された計画と実行のプロセスは、100万個の部品製造あたり、つまり100万個の「機会」あたりの不良件数を確実に少なくするように設計されています。 この低欠陥プロセスの開発手段は、主に問題点を定量的に視覚的に表示する高度な統計分析チャートにある。 リーンシックスシグマはシックスシグマとどう違うのか? その差はわずかですが、それでも重要な意味を持つほど明確です。 まず、リーンシックスシグマは組織全体の効率化に重きを置いているのに対し、シックスシグマは製造業のサプライチェーンに特化しています。 これらは必ずしもガイドラインではなく、あくまで一般論であり、長い時間をかけて証明されたものです。 しかし、2つの哲学の間で共有される技術やツールが増えれば、両者の区別はさらに薄れていくに違いない。 シックスシグマがエラーの特定を優先するのに対し、リーンシックスシグマはエラーの予防を優先する。 また、出力を測定する管理図では、データに現れてから問題を特定することが容易である。 後者のワークフローやカンバン表は、ばらつきを未然に防ぐのに役立っています。 この区別は実際に重要か? 怒らないでください、でも答えはイエス…そしてノーです。 もし、あなたが同僚とリーン原則について何気なく話していて、管理図やばらつきの低減について触れたとしたら、シックスシグマやリーン製造ではなく、リーンシックスシグマと言ったとしても、彼らは混乱しないでしょう(黒帯シグマのカードを持っている専門家は別です、その場合は講義を受ける準備をしましょう!)。 しかし、そうではなく、理論的には、この2つの方法論はほぼ機能的に同等といえるほど重なり合っています。 しかし、本当に問うべきは、実際には、どの業務改善をどのように狙っているのか、ということです。 改善目標とそのためのツールを明確に示すことができなければ、何をきっかけにアプローチしても失敗します。 そうですね、適切な導入とステップアップのためには、これらの別々のアプローチの違いを、実務で発生するように理解し、伝えることが絶対に必要です。 例えば、顧客成功率の向上ではなく、生産プロセスの無駄をなくすことを目標にDoE(実験計画法)を使用している場合、これが無駄の削減という特定の目標を持ったリーンDoEであることを強調し、改善が必要なビジネスの他の領域と関連するリーンシックスシグマ全体のゲームプランにどうフィットするかを説明します。
オン・プレミス
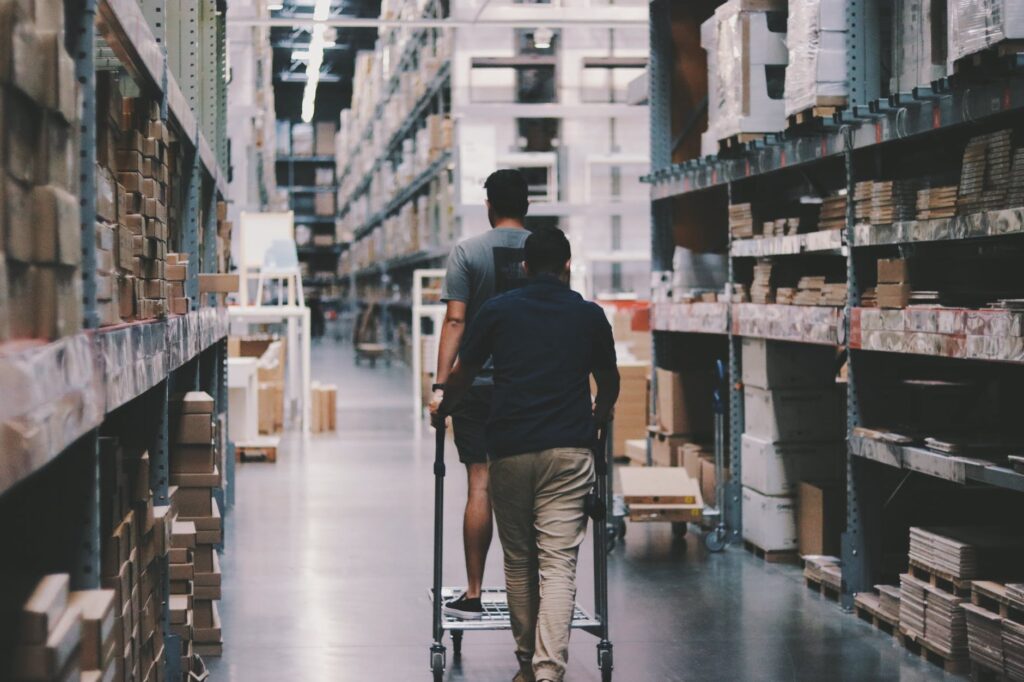
オンプレミスは、オンプレミスまたはオンプレムとも呼ばれ、お客様の所在地に物理的に設置されたプライベートサーバーで独立してホストされるライセンスソフトウェアの一種である。 クラウドコンピューティングを前提としたSoftware-as-a-Serviceの代替となるものです。 キーポイント オンプレース(または「オンプレム」)は、お客様の「敷地内」にインストールされるソフトウェアです クラウド型SaaSの対極にあるもの ITインフラは、オンプレミスソフトウェアモデルの延長線上にあります。 オンプレミスの例 オンプレミスツールには2種類あります: ソフトウェア オンプレムソフトウェアとは、お客様の敷地内にある物理的なサーバーにインストールされ、動作するアプリケーションのことをいいます。 SaaSのような従量課金制とは異なり、ライセンスは物理サーバーにダウンロードされるため、インターネットに接続されていなくてもアクセスすることができます。 オンプレミスソフトウェアの例として、Microsoft Office Suiteが挙げられます。 ハードウェア オンプレミスのハードウェアは、本当に機械のように物理的に存在する道具を表現するための空想的な方法です。 IT環境では、オンプレミスハードウェアの例として、サーバールームにあるハードディスクが挙げられます。 どのような組織や企業でも、通常、オンプレミスのITハードウェアが何らかの形で存在しています。 オンプレミスとクラウド(SaaS)ソフトウェアの比較 オンプレミスとクラウドベースのアプリケーション、どちらのタイプのソフトウェアにも欠点と利点があります。 さらに、ある会社にとって適切なパッケージと、別の会社のソフトウェアソリューションは全く異なるものに見えるかもしれません。 これらのオプションのメリットとデメリットについて読む際には、ご自身のビジネスのニーズを一番よく知っているのは自分自身であることを念頭に置いてください。 例えば、法律事務所では、業務の大半が文書や電子メールアプリケーションに依存する通信業務であり、リアルタイムで常に更新する必要がないため、基本的なMicrosoft Officeスイートのみで運用することが可能です。 (最後にMicrosoft Wordをアップデートした時のことを思い出せるだろうか?それともみんなまだ2010年版を使っているのだろうか?)。 例えば、原材料のサプライヤーが、供給とリアルタイムの課題に応じて流通コストを計算する必要がある場合を考えてみましょう。 オンプレミスソフトウェアのメリット 自社のデータに第三者がアクセスすることがないので、プライバシーの確保に適しているアプリケーションの利用を管理者が完全にコントロールできるサプライヤーからの干渉や予期せぬ自動アップデートなしに、アプリケーションをフルカスタマイズすることが可能 オンプレミスソフトウェアのネガティブな点 社内のメンテナンスと将来のアドオンやアップデートに責任を持つ。APIを自作(または外注)する必要がある当初、専門的な知識を持ったユーザーがいなかったために、ソフトウエアのアプリケーションの能力を十分に発揮できない可能性がある。 SaaSのメリット 従量制で、必要な分だけ容量や処理能力を確保することができる瞬時に拡張でき、他のシステムとの相互運用が可能(複雑なAPIを構築する必要がない)場所を選ばないため、社員は必要に応じてどこからでもデータやファイルにアクセスすることができます。 SaaSのネガ サブスクリプションモデルのシフトにより、短期的なコストが増加する可能性があるソフトウェア・プラットフォーム間で多くの変更がなされた場合、企業が買い物をする際に混乱を引き起こす可能性がある。クラウド経由でデータを保存するため、サイバーセキュリティに不安がある。また、オンプレミスとクラウドの両方を活用したり、あるアプリケーション(物理的な機械を制御するものなど)はオンプレミスで、他のアプリケーション(電子メールなど)はオフサイトで利用するというハイブリッドモデルを選択することも十分可能です。 例えば、VKSの作業指示ソフトは、SaaS型とオンプレミス型があり、クライアントがツールをカスタマイズすることができます。 オンプレミスソフトウェアの要件 ITと管理インフラは、オンプレミスの能力の延長であることを忘れないでください。 つまり、お客様のオンプレミスソフトウェアは、サプライヤーではなく、お客様の責任でメンテナンスする必要があるのです。 もし、他のシステムとの互換性がないなどのインフラ的な問題や、ITスタッフの不足などにより、十分に活用されていないのであれば、その効果は大きく減少することになります。 Microsoft Office 2010を購入し、長年使っていても、突然Microsoftを呼び出して最新バージョンにアップデートするよう要求することはできませんよね。 まず、最新バージョンはもともとダウンロードしたコードに書き込まれているわけではないので、不可能でしょう。 2つ目は、旧バージョンと全く同じ用途であっても、仕様が全く異なる別製品であることです。 これを解決する一つの方法は、コストのかかるハードウェアやソフトウェアの変更を取り入れる前に、IT部門の基盤を構築することです。 また、そのような場合、サプライヤーが提供する管理サポートが追加されるため、SaaSソリューションにこだわることもできます。 また、社内体制を整えた後に、そのソフトウェアでは対応しきれなくなった場合、他のプラットフォームを試すことができるのもメリットです。 しかし、スマートファクトリーの重要なツールセットであるIoTデバイスを理解する上で、オンプレミスとクラウドの違いを認識することは有益である。
ネット・ゼロ・エコノミー
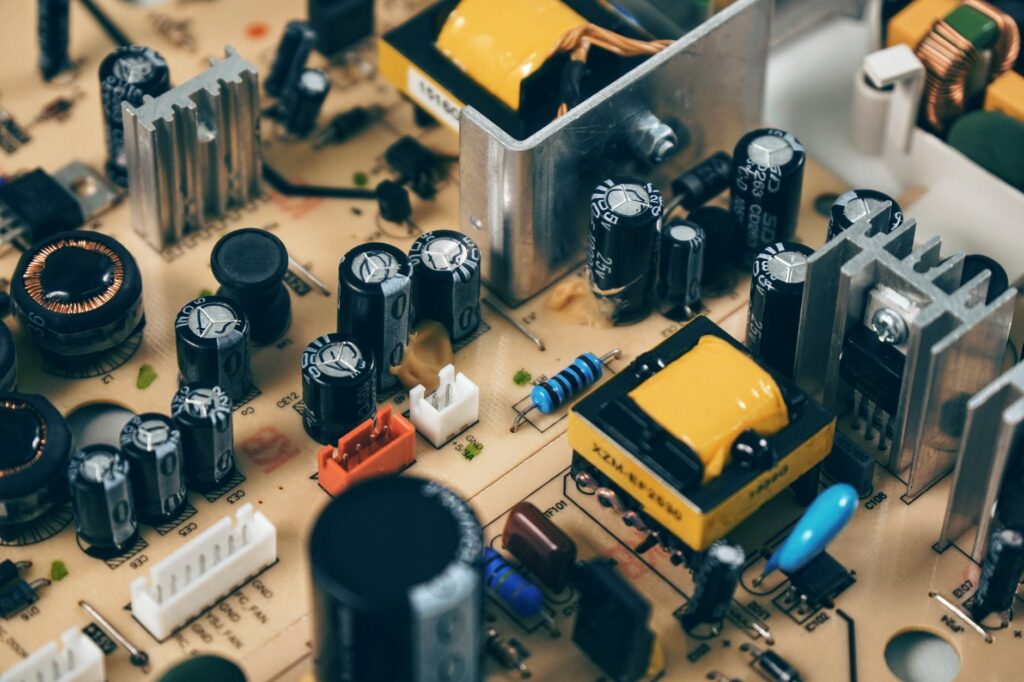
気候変動は、世界の工業生産の分野に劇的な影響を及ぼしており、製造業のリーダーたちはこの課題に対応しています。 グリーン・カラー・ジョブのような持続可能な戦略に投資し、変化に対応することで、グローバルな生産と交換のために構築してきた枠組みを改善することができます。 このトピックのインサイトは、RBC Economics and Thought Leadershipの気候シリーズの最新レポートであるGreen Collar Jobsと、#RacetoZeroキャンペーンに関する国連の2030 Breakthroughsレポートから得られました。 キーポイント ネットゼロは、化石燃料の排出を削減するための世界的な取り組みである 気候変動が深刻化する中、サステイナブルな製造アプローチが必要であり、個人的にも有益である。 グリーンカラー・ジョブとは? グリーンカラー」とは、英語のスラング(俗語)で、さまざまな職業を表す言葉です。 ブルーカラー」とは、建設、農業、製造業などの分野で肉体労働を必要とする仕事のことです(中略)。 ホワイトカラー」とは、通常、事務系の管理職のことで、ホワイトカラーを汚さないような清潔なオフィス環境を指す言葉です。 このスラングは非常に古く、かつては仕事の上流階級と下流階級を区別するために使われていました(それに伴う社会的ライフスタイルや給与の期待値も)。 一方、現代では、職業に求められるスキルや期待が大きく重なり合っています。 もちろん、例えば弁護士が裁判書類の紙を漉くことは通常要求されませんが、特に現代の製造業では、監督者や取締役は、「ホワイトカラー」という時代遅れの言葉から予想されるように、オフィスに座っているだけではない仕事を求められることが多いのです。 それは、「グリーンカラー」というキーワードが加わったことで、産業職の製造方法に関する過去の概念を覆し、気候変動に焦点を当てた産業の前進という視点を変えているのです。 ネット・ゼロ・エコノミーとは何か、なぜそれを追求しなければならないのか? ネットゼロ経済とは、温室効果ガスの排出をゼロにするか、植林や炭素回収などの戦略で排出量を補う経済圏のことです。 ネット・ゼロ・エコノミーを目指すべき理由については、火星の修復が間に合わず、実行可能な選択肢になり得ないと思います。 ネットゼロがあなたのビジネスにとって優先されるべきかどうかわからない場合でも、環境的に持続可能であるための小さな役割を果たすこと以外にも、以下のようなメリットがあります: 生産サイクルのリーン化・効率化サステイナビリティに対するコミュニティーの評判が良くなる石油・ガスからクリーン電力への切り替え時の全体的なコスト低減市場の変動やサプライチェーンの混乱への対応力向上世代を超えた未来志向の会社づくりグリーン雇用の創出と技能訓練による、自社の雇用市場への投資グリーン・イニシアチブまたはグリーン・カンパニーに対する税制および機会のメリット ビジネスにおけるコンピュータの導入と同じように、グローバル産業は必然的にこの方向に向かっており、遅れをとらないためには、大手企業が使っている新しい技術や方法論(NFTのような新しい流行という意味ではなく、データに裏付けられた戦略や賢い組織再編のこと)を学ぶ必要があります。 COVIDの大流行とその後のインフレ経済が、一部の企業に大きな打撃を与えたことを考えれば、一息ついてもいいのではないでしょうか。 これにより、タスクとオペレーションが適切に標準化され、将来にわたって持続的に改善するための最適なリーンフレームワークが実現します。 個々の企業がグリーンカラージョブに投資するには? 大きく分けて4つのカテゴリーがあり、大きく分けて投資可能な分野を表しています: グリーン企業における新しいスキル(新しいスキルを必要とする新しいグリーン技術に対応するオペレーターなど)グリーン企業における既存のスキル(例:新規グリーン企業における従来の事務職の役割)既存のスキルに対する需要の増加(例:技能労働者がスキルをより広く応用する、別名マルチスキル化)既存の仕事における新しいスキル(アップスキルなど)。 例えば、サステナブル・ソリューションを主要なサービスや商品とする新興企業でなければ、現在の従業員のスキルアップや、部門間の管理上の無駄の程度を評価することから始めればよいのです。 グリーン・カラー・ジョブの創出とは、古い従業員を解雇し、「環境」を意識した新しい従業員を採用することではなく、ペーパーレスの標準を導入することによってホワイトカラーやブルーカラーの仕事をアップグレードすることであり、従業員にコストだけでなく、物流における特定の輸送ルートの環境への影響を評価することを奨励することだからである。 本来はここで、自社のスタイルに合ったものを工夫するのが良いのでしょう。 化石燃料の使用から撤退することもそうですし、排出量を相殺するために文字通り植林をするチームを結成することもそうです – Wild and go green! グリーンになるためのタイムラインは? この答えが腹立たしいように、昨日のことなんです。 特にネットゼロ経済については、2050年までにすべてのG7諸国(カナダ、英国、米国、ドイツ、イタリア、フランス、日本)が、他の120カ国以上とともにネットゼロ排出を約束した。 優れた経営手法が説くように、次のステップは、目標を段階的に分解し、成功のたびにゴールポストを設定して、進捗状況を把握することです。
ミックスド・モデル・アセンブリ
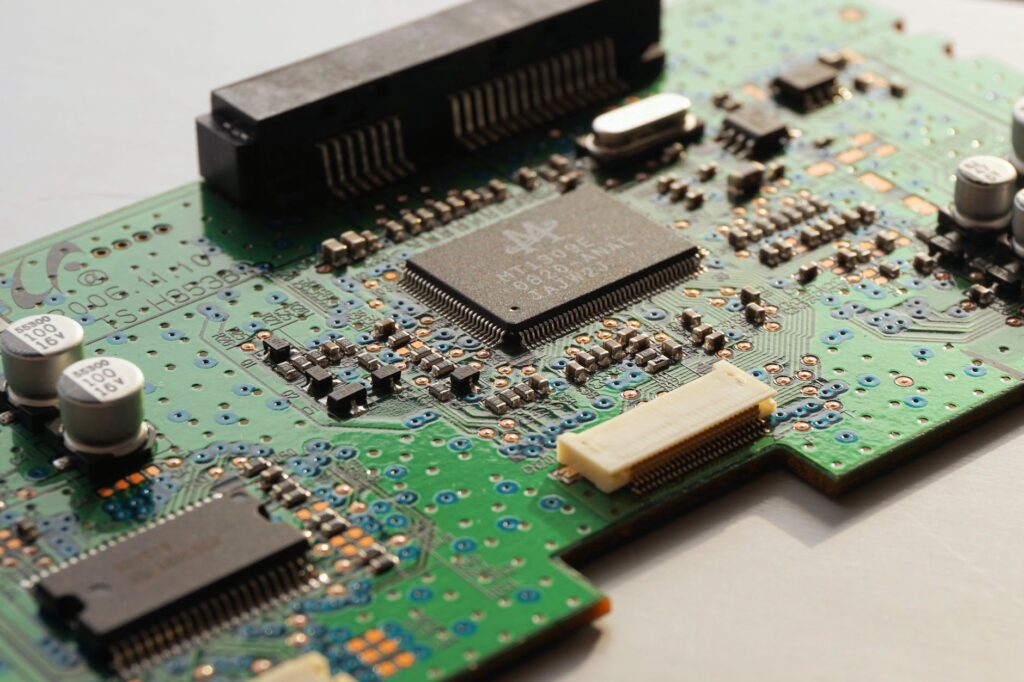
ミックスド・モデル・アセンブリとは? 生産性、効率、品質を低下させることなく、1回の作業で複数の異なる製品またはモデルを生産する生産システムの一種である。 このような環境では、1つのラインで作られる製品の数は、数十万バリエーションに達することもあります。 生産されるモデルの頻度や仕様は、各製品の特定の需要に大きく依存します。 そのため、ある製品は頻繁に生産ラインに登場する一方で、ある製品は半年から1年に1度しか登場しないこともあり得ます。 一品生産のように、モデルの組み立てが一度しかできない場合もあります。 その後、ラインは新しい組み立て作業に切り替わります。 これに対して、大量生産型の組立ラインでは、1~2個の製品に絞って生産します。 組立ラインは、すべての行動、設備、材料が一つの連続した流れに標準化された環境の中で製品を生産するものです。 多くの混流メーカーにとってホットな話題は、「混流組立ラインの中で、いかにして標準化の強みを維持するか」ということです。 キーポイント 混合型組立ラインは、現在の市場の多様な需要に対応するため、さまざまなモデルや製品を生産しています。 混合モデル組立の最大のメリットは、多様な需要の流れに対応できることです。 この生産システムの最大の課題は、多くの異なる製品ラインを生産するという複雑さが増すことです。 スマートな製造業は、作業指示ソフトウェアを統合することで、これらの課題を軽減しています。 なぜミックスモデルアセンブリなのか? まあ、これはちょっと複雑で、製造業の歴史を見る必要があるんですけどね。 第2次産業革命の動く組立ラインをご存じでしょうか。 T型フォードのような1つの製品が、動く組立ラインを移動しながら、固定された作業者が同じ動作を何度も繰り返していく。 これにより、次の100年以降も使用され、改良されることになる標準的な方法が作られたのです。 これは画期的なことですが、問題がありました。 お客さまは、バリエーションがまったくないフォード・モデルTしか手に入れることができなかったのです。 外装色も黒だけに限定された。 しかし、100年以上の技術やプロセスの進化に伴い、顧客は製品により多くのバリエーションを求める一方で、購入する製品のライフサイクルをあまり重要視しなくなりました。 そして、アマゾンなどのオンラインショップが大型店の3,000倍近い商品を扱うEコマースの導入により、市場は大量の商品バリエーション、カスタマイズ、選択肢に慣れました。 そのため、常に動き続ける新しい製造環境、柔軟性が求められる製造環境になっています。 最後に子供のおもちゃを買ったときのことを考えてみてください。 もはや、上3段の棚全体を貫くのは、1台の赤いトラックです。 その赤いトラック、青い車、黄色いSUVは、すべて何千ものブランドからオンラインでアクセスできます。 そして、これらのおもちゃのほとんどは、人形、プレイハウス、BBQ、パティオ家具、産業用シェルビングユニットなどのバリエーションも作っているブランドやメーカーから発売されています。 また、製品ラインナップを増やす一方で、古い製品を削除する可能性も低く、お客様の選択肢の幅が広がります。 一部の製品やブランドでは依然として大量生産が不可欠ですが、将来的に接続されたグローバル市場の拡大傾向には、混合モデルの組立ラインが不可欠です。 ミックスモデル組立の長所と短所トップ3 混合モデルの組み立てラインには、主な利点がある一方で、主な課題もあります。 それぞれの課題には重要な利点があり、その逆もまた然りです。 そのため、この生産方式が最適かどうかは、製品、想定する市場、ビジネスの目標や戦略によって大きく異なります。 このような背景から、ここでは混合型組立ラインの長所と短所のトップ2、そして長所を高め、短所を軽減する方法を紹介します。 トップ2のプロフェッショナル さまざまな収益源に出会うより安価で、より効率的な在庫これらを少し紐解いてみましょう。 混合モデル組み立ての主な利点は、柔軟な対話ができることです。 顧客のニーズや新たな収益源に合わせて生産ラインを素早く変更できる企業は、新たな課題に立ち向かい、新たなチャンスをつかむことができる。 卵は一つのカゴに盛るな」という言葉をご存知でしょうか。 ミックスモデルアセンブリはまさにそれです。 また、在庫の面でも、需要に応じて生産ペースを決めるプル型生産方式を採用することで、より少ない在庫を保有することができます。 顧客の要求に応じて、製品の構成、ペース、量を決定するため、混合型製造業は在庫を数分の一に減らすことができるのです。 トップ2の欠点 より大きなマネジメントと戦略を必要とする労働者を混乱させる可能性がある混合モデル組み立ての主な欠点は、管理が難しいことです。 混合モデル組み立ての利点のほとんどに、複雑な層が追加され、その結果、管理するのが難しくなることがあります。 多様なプロセスには、多様な課題があります。 さらに、作業者が自分の具体的な業務に戸惑うこともあります。 第2次産業革命の動く組立ラインの話に戻ろう。 すべての作業者が1つの作業を、シフトの間ずっと繰り返していたのです。 超絶退屈で単調ではあるが、混乱するスペースはほとんどない。 一方、ミックスモデルの組立工は、ほぼ毎日違う作業をしています。 また、ある種の作業は頻度が低いため、作業者がその作業のやり方を十分な程度に記憶することは困難です。 […]
資材所要量計画(MRP)
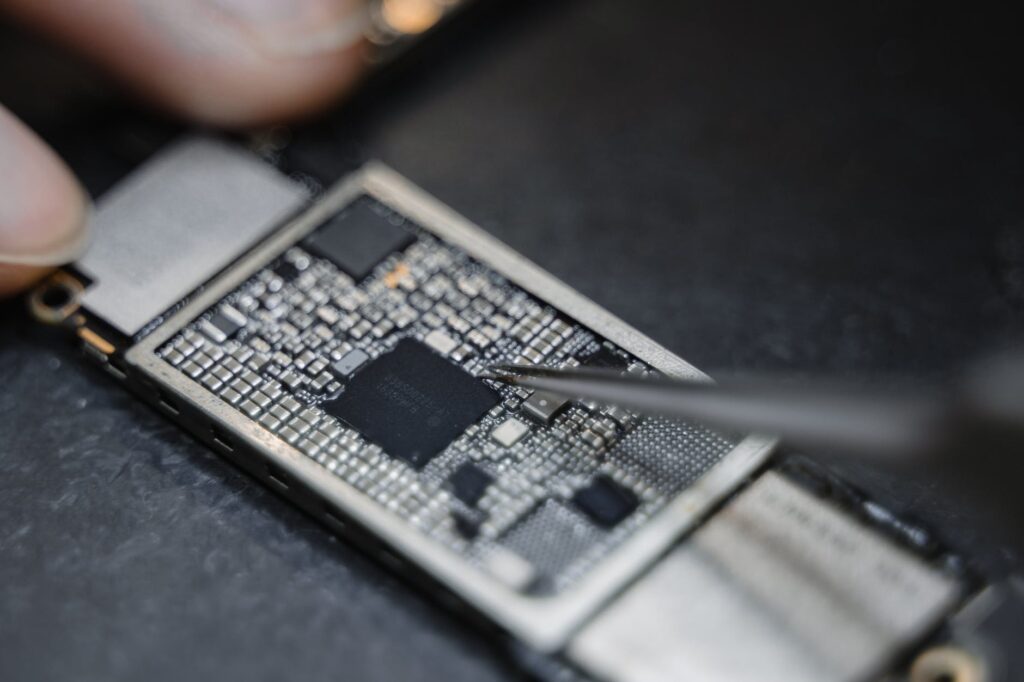
MRP(Material Requirements Planning)とは何ですか? 資材所要量計画とは、企業が製造工程や資材の使用量をより効率的に計画、追跡、スケジュール、監視できるようにする在庫管理システムです。 MRPは通常、3つの主要な目標を掲げています: 生産に必要な材料や部品が常に入手できるようにする。最初のルールを守りつつ、材料や部品のレベルをできるだけ低くする。適切な製造スケジュールと計画を作成する。企業はMRPを使って、どんな材料が必要なのか、特定の仕事にどれくらいの量が必要なのか、いつ納品が約束できるのかを見積もる。 MRPは適切に導入されれば、運用コストを削減し、効率を高めるとともに、大量の在庫を必要としなくなります。 キーポイント MRPとは、製造業がリソースを正確に把握し、生産スケジュールや納期を設定し、リソースの使用量や生産量を監視するためのツールである。 すべてのMRPは、部品表(BOM)から逆算して、最終製品を作るために必要な資源要件を策定します。 マテリアル・リクワイヤメント・プランニングは、3つの重要な質問に対応します:何を、どれだけ、いつまでに? MRPは、在庫コストを削減しながら、効率と生産性を向上させます。 MRPはどのように機能するのか? MRPを理解するのに役立つのは、「後戻りするシステム」と考えることです。 MRPは、完成した製品の生産計画から、最終製品の製造に必要なサブアッセンブリー、コンポーネント、原材料のリストに変換するものです。 決められたスケジュールを守りながら。 私たちは、あらゆる制作物の「何を」「いくらで」「いつまでに」を見ることで、これをマッピングすることができます。 すべてのMRPは、この3つの問いを核にしています。 必要な素材は何ですか?素材はどのくらい必要ですか?素材はいつ頃必要ですか? MRPの4つのステップ 上記の3つの質問を実行可能なアイテムに変換するには、4つの基本ステップが必要です。 必要な資材を見積もる:最初の作業は、プロジェクトの材料需要を決定することです。 資材所要量計画では、最終製品に必要な原材料をまとめた部品表案を検討します。材料を探す:次に、MRPは最終製品の材料を探す必要があります。 そのために、すでにある在庫をしっかり見て、どの材料が必要かをチェックします。 そして、すべてのプロジェクトが必要な素材を確保できるよう、適切な部署にリソースを配分しています。制作スケジュールを立てる素材が見つかったら、次は適切な納期を算出する。 プロジェクトや最終製品を完成させるために、どれだけの時間や労力が必要なのか。プロセスをモニターする最後に、プロセスを監視することです。 遅延や材料の問題が発生した場合、優れたMRPシステムはすべてのコンポーネントを追跡し、それに応じてリソースを再配分する機会を提供します。 MRPのメリットとデメリット MRPのメリット すべての仕事において、必要なときに必要な材料、消耗品、部品が揃っていることを確認する。在庫を多く持つ必要がなくなる。業務効率と生産性の向上。リードタイムが短くなる顧客満足度の上昇。MRPシステムの代表的なメリットは、必要なときに必要な材料が手に入るという保証があることです。 必要な時に必要な素材があれば、大量の在庫を抱えたり、資源を備蓄したりする必要がありません。 これにより、業務効率と生産性が向上し、リードタイムの短縮や顧客満足度の向上が可能になります。 MRPのデメリット 現代のMRPはメリットがかなり多いのですが、デメリットもないわけではありません。 計画は、生産スケジュールに関しては、厳格で容赦がないものです。収集したデータは、正確でなければ機能しません。MRPシステムは、導入が難しく、コストがかかることが多い。MRPシステムで最も多い問題は、柔軟性の低下につながることです。 生産スケジュールを最適化する包括的な計画を立てるのはいいのですが、計画通りにいかないときに、メーカーはどれだけ対応し、柔軟に対応できるでしょうか。 同様に、MRPは正確で精密な情報の収集に依存しています。 情報が間違っていれば、システムは効果のない計画を立ててしまう。 そして最後に、MRPは高価なものである可能性があります。 ERP(統合基幹業務システム)ほど高価ではありませんが、MRPは高価です。 つまり、確実なメリットがあるにもかかわらず、メーカーはこれをコストと天秤にかけて判断する必要があるのです。 MRPとERPの比較 MRPとERPは、表面的にはほとんど同じことをやっているように見えるかもしれません。 そして、両者はいくつかの点で共通していますが、同じものにはほど遠いのです。 これまで述べてきたように、製造業にとって資材所要量計画は、在庫管理、生産能力計画、スケジューリングのための優れたツールです。 一方、ERPはこのアプローチをさらに推し進め、バックオフィスのビジネス機能を自動化することで、メーカーが経営をよりコントロールすることを可能にします。 それでは、現代のMRPとERPの主な担当業務を簡単に説明します。 MRPの責任 在庫管理、サプライチェーンマネジメント、生産スケジューリング、資源配分。 ERPの責任 在庫管理、サプライチェーン管理、生産スケジューリング、資源配分、会計、製造オペレーション、顧客管理、品質管理、プロセス戦略。ERPは、MRPとほぼ同じ役割を担っており、責任範囲が非常に広いことがわかります。 しかし、MRPは現代の製造業において、依然としてその役割を担っています。 注意すべきは、ERPがMRPを置き換えるわけではないということです。 ERPには資材所要量計画機能が組み込まれていることが多いですが、ERPのような複雑な機能を必要としないメーカーにとっては、スタンドアロンMRPが便利です。 従来、資材所要量計画システムは、製造業を中心とした中小企業で利用されてきました。 […]
PDCAサイクル
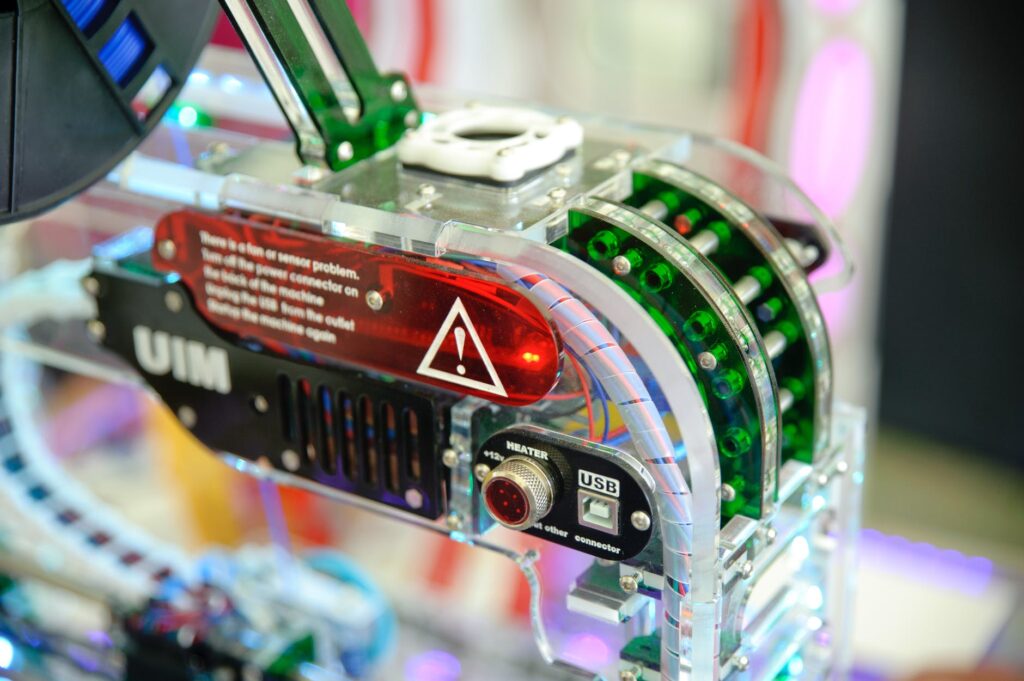
PDCAサイクルは、継続的な改善のステップをプロジェクトごとに計画し、区別するためのシンプルかつ効果的なツールです。 PDCAサイクルは、シックスシグマやトータルクオリティマネジメントの経営理念でよく使われる反復的なツールです。 キーポイント Plan-Do-Study-Act、Deming、Shewhartサイクルとも呼ばれる。 4つのステップPlan、Do、Check、&Act PDCAを回すことでカイゼンを促す。 チームが継続的な改善を重視すると言うのは簡単ですが、長期にわたって実行するのは難しいものです。 PDCAサイクルは、カイゼンを4つの管理可能な領域に分解することで、従業員を循環的な改善パターンに導くのに役立つ。 PDCAサイクルのバリエーションが生まれた歴史的背景 PDCAサイクルの最初の事例を特定するのは、やや困難です。 このサイクルは、20世紀半ばに活躍した統計学者であり、革新的な経営指導者であったウィリアム・エドワーズ・デミングに由来するとする説が有力です。 デミングは、師匠であるウォルター・A・シューハートからインスピレーションを受け、当初このプロセスを “シューハート・サイクル “と名付けました。 やがて、PDSA(Plan-Do-Study-Act)サイクルと呼ばれるようになり、時には「デミングホイール」とも呼ばれるようになりました。 しかし、この循環型プロセスの起源はさらに遡り、フランシス・ベーコン卿が開発した科学的手法にあります。科学的手法は、体系的な実験と論理的な結論によって仮説を検証することに重きを置いています。 PDCAは何のためにあるのか? PDCAサイクル、または関連する頭字語はどれでも構いませんが、一般的に4つの発展段階があります: ステップ1:計画 科学実験のプロセスや仮説、必要な材料、導入研究の概要を説明せずに実験を始めることはないでしょう? そのため、重要な生産工程を修正・改善しようとする場合、余計な変数に手を加える前に、完全な攻撃計画を概説することが賢明である。 計画段階は、PDCAサイクルの他の重要な段階で選択するための選択肢のマップを持つために、可能な限り詳細な情報を提供する必要があります。 優れた科学者は偶然を見逃さず、優れた経営者はあらゆる可能性を考慮し、迅速に適応して無駄を省く。 ステップ2:Do PDCAサイクルを回す際にリーダーが陥りがちなのが、「Doing」の部分を強調しすぎることです。 たとえそれが非常に魅力的で能動的なステップであっても、変化を実行すること(すなわち「実行すること」)は、計画段階の二の次であるべきです。 このステップを予想以上に小さくする理由は、このステージで使用するすべての行動計画は、事前にプランニングで確立されていなければならないからです。 Doingは、計画プロセスの延長に過ぎない。 PDCAサイクルは、教科書のエッセイのようなものだと考えてください。最初の段落では、メイントピックや仮説など、取り上げたい概念を紹介します。 そして、第2パラグラフでは、イントロダクションで取り上げたコンセプトをさらに発展させています。 農業技術に関するエッセイを読んでいて、著者が突然スーパーマーケットのサプライチェーンの話に切り替えたとしたら、その微妙なつながりはわかるかもしれませんが、著者の主張の本筋がわからなくなってしまうでしょう。 PDCAサイクルは、トピックからトピックへとあちこち飛び回ることでわかりにくくならないように、計画段階の続きを論理的に追い、サイクル全体のマップを頻繁に参照するようにしましょう。 ステップ3:チェック PDCAサイクルの第3ステージは、第2ステージで発生した「やる」ことの結果を「確認」することです。 デミングは、この第3ステップを「チェック」ではなく「スタディ」と呼んだと言われていますが、プロセス改善の種類によっては、どちらも適切です。 このステップの目的は、プロセス実験から得られたデータを検証することです。 これは、いくつかの異なる方法で行うことができます: 新しいプロセスを監査するために第三者に依頼し、ギャップがないかをチェックする。実験プロセスを同様の条件で繰り返し、確実に効果を出すこと異なる条件下で実験プロセスを繰り返し、プロセスの効果の限界を検証する。プロセスの拡張性を検証するために、範囲と参加者を拡大する。自社データと、成果が実証されている査読付き研究との比較データを「チェック」する方法はさらにたくさんあるので、プランニングセクションの中で、どのデータセットをどのように定量化するのか、幅広い質問をするようにしてください。 ステップ4:行動する 第4ステップの「行動」は、テストされ承認された変更を実行することと、その変更の長期的なモニタリングを確立することの2つの重要性を持っています。 プロセスが改善され始めたら、その改善水準を維持するための基準を導入し、次のプロセス改善へとつなげたいものです。 先回りして結論を出すようなマネジャーにはならないようにしましょう! あなたのチームがPDCAサイクルの段階を丹念に回しているのは、最初から正しく行い、時間をかけてプロセスを自給自足させたいからです。 PDCAサイクルの活用によるメリット PDCAは、組立ラインのカイゼンや部門間の責任分担の見直し、さらにはまだ導入されていない新基準の実験に使うなど、ほぼ普遍的な応用が可能です。 ここでは、観察可能な効果の一部をご紹介します: リーダーシップの停滞期からの脱却をサポート改善を追求する風土を醸成する進行中のプロジェクトの今後のタスクを明確化する大きな変化を起こす前に、小規模なテストを行う標準化を実現します。イノベーションを促進する創造的な問題解決と実用的な解決策を奨励する。 PDCAループを閉じる:次に来るのは? PDCAループは1つのプロジェクトを指すものであり、プロジェクトごとにサイクルを分けることで、タスクの分割や進捗の確認が容易になります。 しかし、終わりのないToDoリストからようやく何かをチェックできたときの喜びはひとしおで、新しく改善された生産工程を、PDCAの手法によって「修正された」と思って放棄する誘惑もある。 継続的な改善には終わりがない! だからこそ、新しいプロセスを監視するために、他の人が最終的にターゲットになるようなチェックとバランスを実装することが非常に重要です。 システムという以上に、サイクルなんです! 大きなプロセスを、計画、テスト、チェックといった小さな段階に分けることで、有益な変化を維持することが管理しやすくなり、追跡も容易になります。